rmm727
New member
I had this Razor E300S scooter given to me some time ago. The batteries were bad and it didn't come with a charger so I decided to put a smaller gas engine on it. I had a 2 stroke Tecumseh snow blower engine that I wanted to use but its mounting method and stepped crankshaft posed some difficulties in coming up with an engine mount that wouldn’t drastically alter the scooter frame. Fast forward a bit and I now have a g100 clone from a Baja DB30 mini bike. It is slightly smaller than the Tec 2 stroke, installs in a more conventional way, and had the clutch already mounted. Now that I had the engine mounting somewhat figured out, I decided to move on to the next problem... the rear wheel sprocket. These Razor scooters use a #25 chain sprocket mounted to a freewheel.
I decided to remove the freewheel and replace it with a #35 A type sprocket or a plate sprocket to some folks. The sprocket has 35 teeth and a ½” bore. I had a machinist friend bore the center to provide a slip fit over the freewheel threads. I also had him drill the (3) 6mm holes on a 60mm bolt circle.
Now that was out of the way, I measured and cut some hex stock to act as spacers. Fearing that the small 6mm bolts wouldn’t be able to handle the stress of having a sprocket attached to them, I cut 3 pcs of 3/16” x 1” band iron to tie the hex spacers together. I felt this would keep the bolts from shearing or bending.
Some more pics for now.
Need to finish welding the spacer, sandblast, and paint it. Also need to see if my hardware store has socket head caps screws in a length that will work for this. Then on to the engine mount.
I decided to remove the freewheel and replace it with a #35 A type sprocket or a plate sprocket to some folks. The sprocket has 35 teeth and a ½” bore. I had a machinist friend bore the center to provide a slip fit over the freewheel threads. I also had him drill the (3) 6mm holes on a 60mm bolt circle.
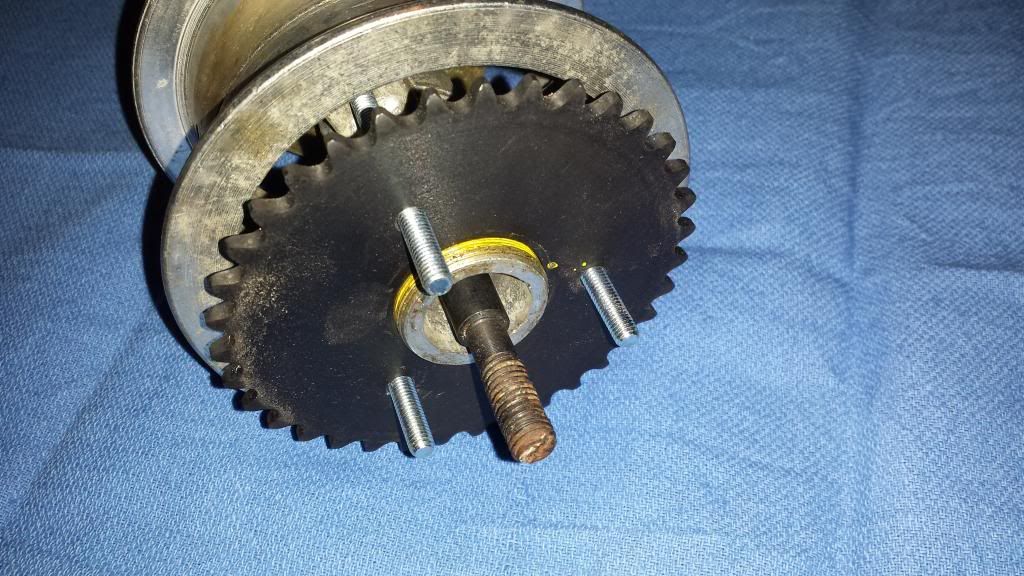
Now that was out of the way, I measured and cut some hex stock to act as spacers. Fearing that the small 6mm bolts wouldn’t be able to handle the stress of having a sprocket attached to them, I cut 3 pcs of 3/16” x 1” band iron to tie the hex spacers together. I felt this would keep the bolts from shearing or bending.
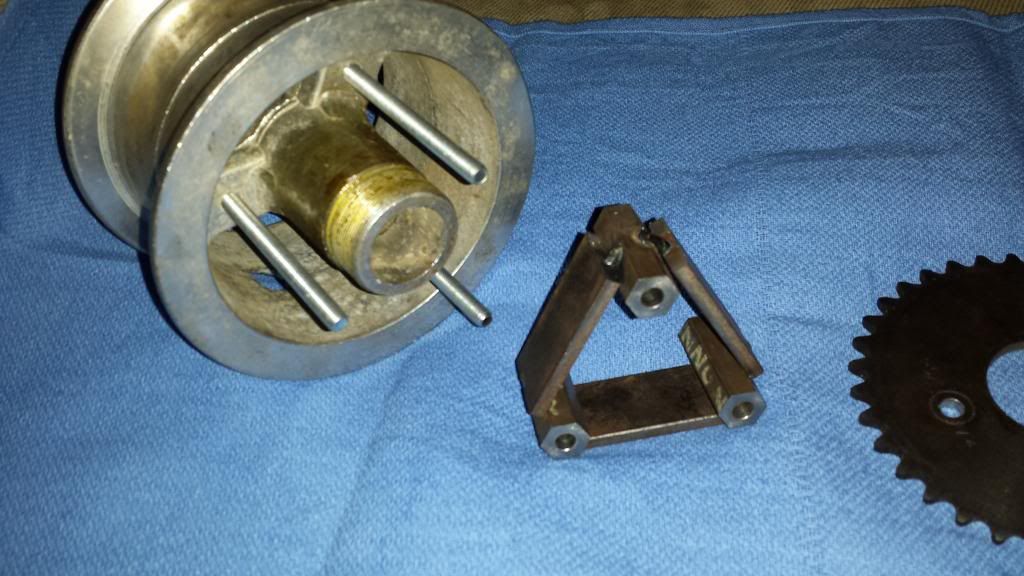
Some more pics for now.
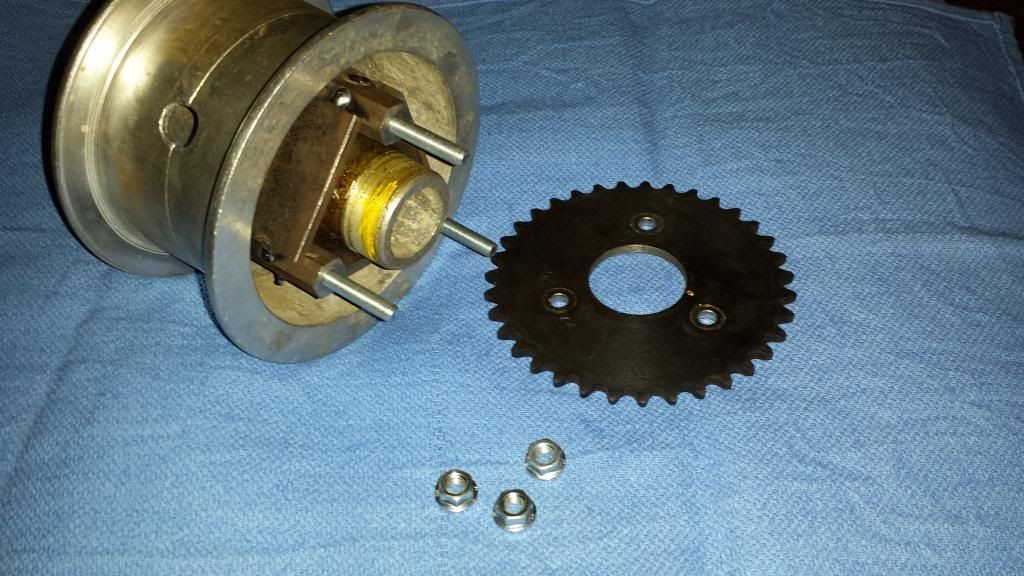
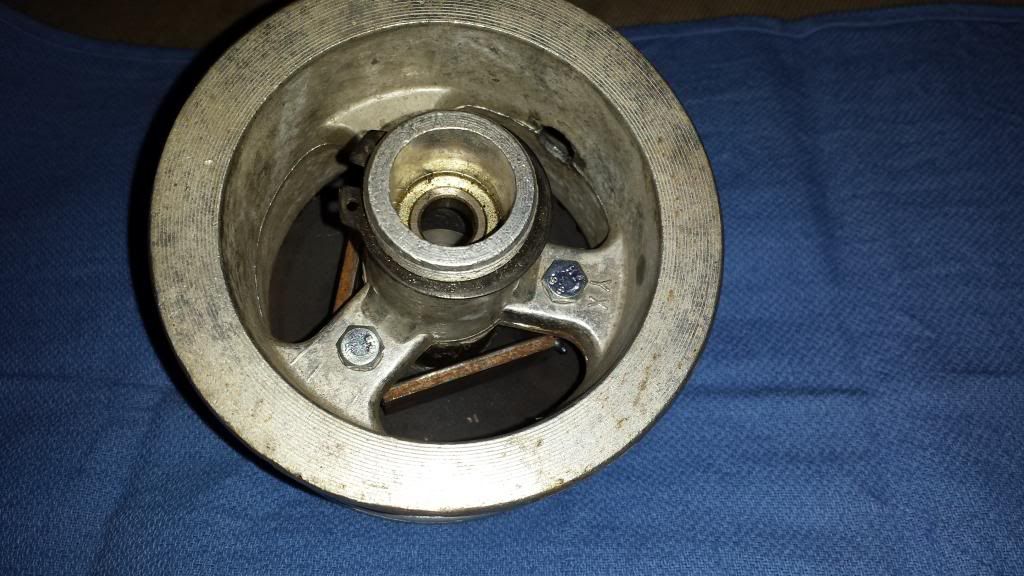
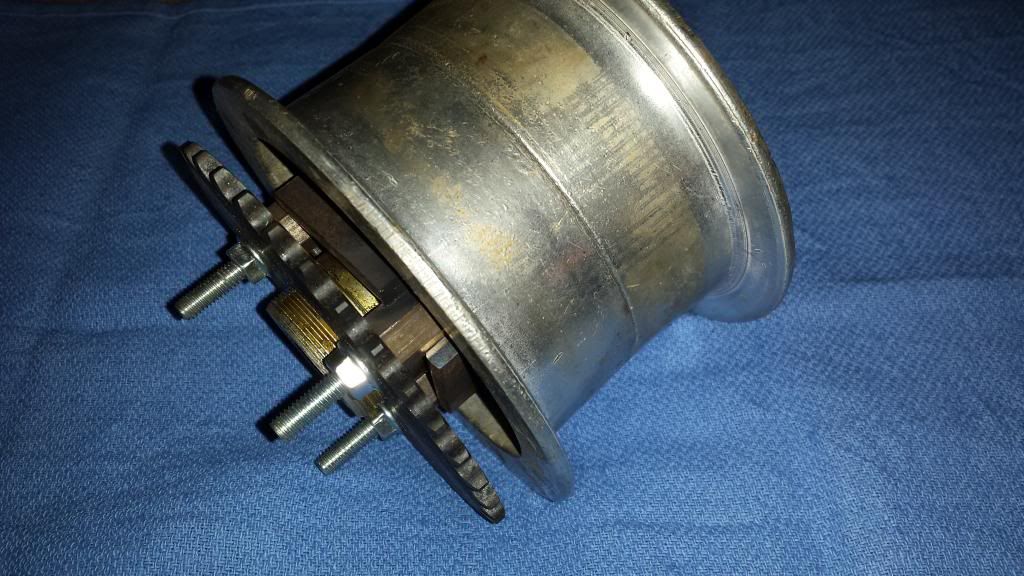
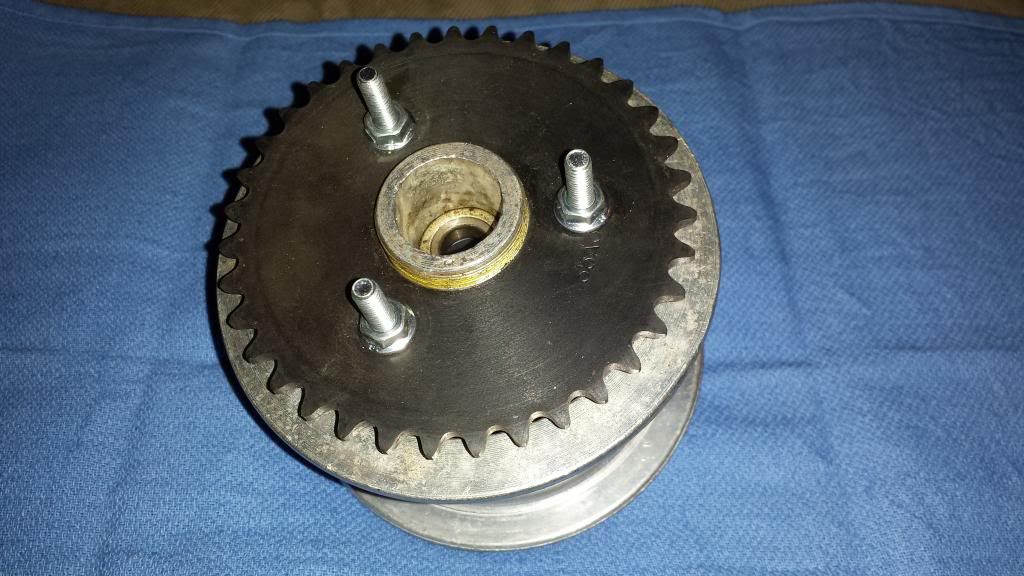
Need to finish welding the spacer, sandblast, and paint it. Also need to see if my hardware store has socket head caps screws in a length that will work for this. Then on to the engine mount.